With the development of aerospace manufacturing technology,Aerospace product structures are becoming more complex, with rising accuracy requirements.
To increase the effective load, the parts themselves are becoming lighter and lighter.
Deep-cavity thin-walled parts are lightweight, mechanically strong, and evenly load-bearing, boosting their use.
A deep-cavity thin-walled part requires high accuracy, is made of aluminum, and has high metal removal, large residual stress, and a small clamping area.
During processing, issues like deformation, back arc clamping difficulties, tool wear, and poor surface quality arise.
This paper applies dynamic milling for deep cavity thin-walled parts, optimizes clamping, and addresses stress release.
Optimizing milling parameters effectively controls part deformation, reduces roughing time, boosts efficiency, and solves machining issues.
Processing status
Product structure analysis
The part has a wall thickness of (3±0.05) mm, depth of 57 mm, a 9 mm thick circular arc bottom, and a 180 mm chord length.
The part structure in Fig. 1 shows the bottom arc surface, which must meet a dimensional tolerance of 9 ± 0.05 mm for high accuracy during machining.
Processing difficulties
The aluminum structure is machined from a single 2A14 aluminum forging.
The workpiece structure and material pose four challenges: high metal removal rate (up to 95%), uneven residual stress, tool wear, and clamping difficulties.
Large metal removal rate
With a 95% metal removal rate, optimizing the roughing process and cutting parameters reduces vibration and surface roughness, ensuring high milling efficiency.
Large deformation
The part features a 51 mm deep cavity and thin walls,Leading to deformation due to the low rigidity of the open thin-walled structure.
It is very easy to produce machining deformation during machining, and it is impossible to guarantee the milling accuracy.

Serious tool wear
With a cavity depth of 51 mm, the tool length must exceed 51 mm, leading to serious vibration and increased corner wear.
Difficulty in clamping the back arc
Back-arc machining is challenging to clamp, and deformation of the bottom arc surface is difficult to correct, risking accuracy loss and potential scrap.
Machining program
Process program after the introduction of dynamic milling
Positive clamping: 5 mm process edge is clamped in a hydraulic vise.
Roughing with D12R2, dynamic, contour, and bevel roughing, arc and bevel finishing, R2 cleanup, final finishing.
Reverse clamping, support tooling setup and fixture inspection, back arc roughing, semi-finishing, finishing, subsidence finishing.
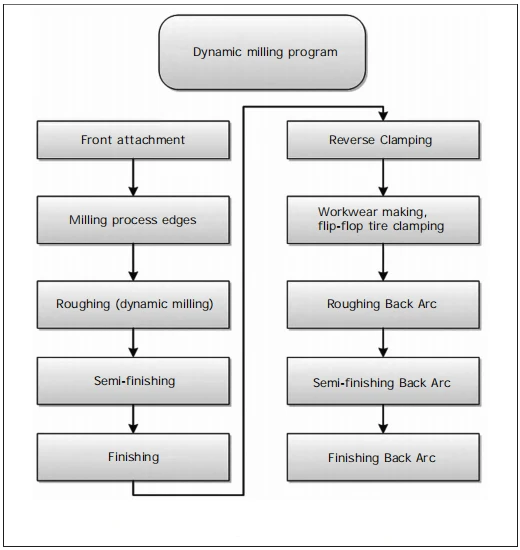
Masrtercam dynamic milling strategy
Efficiency is measured by Q = (ap – ae) * vf / 1000. Large ae in conventional cutting increases force nonlinearity.
Dynamic milling minimizes cut width and tool impact, maintains stable cutting forces, and allows deeper cuts.
Optimized feed rates in dynamic milling boost removal, ensure consistency, and enable fast, stable machining.
Drawing on CNC competition experience, we used Mastercam’s dynamic milling to cut roughing time in half for deep-cavity thin-walled parts.
Dynamic high-speed machining is stable, improving stress relief, accuracy, and efficiency while reducing costs compared to traditional milling.
Smooth cutting and full stress release
Less side milling smooths cutting, lowers impact, releases stress, reduces deformation, and improves accuracy.
Traditional XY-layered corner cutting causes over/undercuts from speed changes and compensation errors.
Excessive tool overhang in deep cavity machining amplifies vibration, leading to corner overcutting.
Dynamic milling uses arc-shaped tool paths in corners, keeping side cutting low.
This process gradually releases internal stress, minimizing deformation, reducing tool vibration, and nearly eliminating corner overcutting (Figures 3 to 6).
High milling efficiency
Dynamic machining uses smaller tools for corners, lowering overcutting but reducing efficiency. Dynamic milling boosts depth and removal rate.
Greater cutting depth, faster feed, and less side cutting boost high-speed roughing. Table 1 shows optimal conventional vs. dynamic milling.

Traditional XY-slotting with a φ12 tool (ap 3 mm, ae 9 mm, vf 1600 mm/min) yields Q = 54 cm³/min.
Dynamic milling with a φ12 tool (ap 30 mm, ae 2.4 mm, vf 2000 mm/min) achieves Q = 172.8 cm³/min, boosting efficiency by 320%.
Long tool life
Dynamic milling reduces cutting forces, stabilizes cutting, and minimizes tool-workpiece contact, improving chip removal and heat transfer.
Improved heat dissipation reduces the impact force during tool cutting, decreases tool wear, and extends tool life.
Dynamic milling by reducing the width of cut to improve heat dissipation, to achieve the purpose of reducing tool wear and extending tool life.
Dynamic machining causes less tool wear, with tool life 1.9 times longer than conventional methods.
Manufacturing tooling
To machine the curved back surface, we design internal support tooling (Fig. 7) with asymmetric, error-proof, one-way clamping.
We clamp the outer cavity to the tire, measure the tire gap with a stopper in its natural state, and then measure the tire again after clamping.
Rough machining the back arc, semi-finishing with a plug gauge, and measuring wall thickness with an acoustic gauge.
Optimized cutting parameters
Cutting line speed VC= π-DC-N/1000; spindle speed N=VC-1000/(π-DC); feed rate Vf =f-z n-zn; metal removal rate Q=ap-ae-vf /1000.
To find the optimal machining program, we conduct experiments to verify it. We summarize the orthogonal experiments in Table 2.

After the orthogonal test, we determine that the dynamic axial depth of cut ap, which is 2~3 times the tool diameter, provides the best result.
The cutting conditions of the 6th group of experiments are good, the surface quality is good, and the unit metal removal rate is large.
Machining effect
We optimized the process, clamping, and parameters, achieving Ra 3.2 μm roughness and 0.03 mm sidewall error, meeting the (3 ± 0.05) mm precision.
Conclusion
Mastercam’s dynamic milling is increasingly used in global CNC competitions and factory applications for its high efficiency and low consumption.
Dynamic milling offers high removal rates, stress relief, and low tool wear, making it ideal for deep cavities and hard materials.
This method shows strong potential for controlling machining deformation, releasing residual stress, and improving the efficiency of full-part machining.